During the second Dail debate February 1963, Mr Jack Lynch Minister for Industry and commerce :Ammonia contains over 80 per cent pure nitrogen. Part of the ammonia produced at the Arklow factory will be used for reaction with sulphuric acid produced at the factory to manufacture sulphate of ammonia. Ammonia will also be used for the production of calcium ammonium nitrate, the second main product of the factory, which indeed is expected to become the main product of the future. The manufacture of calcium ammonium nitrate involves the production of nitric acid from ammonia. The reaction of this nitric acid with additional ammonia gives ammonium nitrate, which, as a pure dry product, contains about 34 per cent pure nitrogen. The nitrogen content is reduced while the product is still in slurry form by mixing the product with finely ground limestone. This treatment ensures that there can be no danger of fire or explosion which could happen in certain conditions with pure ammonium nitrate. The grade currently favoured by Irish farmers contains 20.5 per cent. Nitrogen, but the indications are that calcium ammonium nitrate containing 23 per cent. and perhaps 26 per cent. Nitrogen is likely to find favour in the foreseeable future. These higher concentrations can readily be produced at Arklow 1968 Advert for N.E.T. Ammonium Sulphate 21%
From the Wicklow People 1973
Progressive N.E.T. is striding ahead
How a Giant was born
When the Howard family acquired Shelton in the 1660’s the events to take place there 300 years later were beyond the bounds of imagination, for the 1960’s saw the culmination of long and careful planning for the establishment of a giant fertilizer complex between Shelton entrance and the River Avoca. Nitrigin Eireann Teoranta came into being in 1961 and the original N.E.T. staff spent most of the next year, with the help of consultants, in negotiations with various contractors. This resulted in innumerable flying visits to Arklow by foreign technical experts to study the ground at first hand; the borehole men also arrived to carry out tests. Apart from these visits, there were no signs of the forthcoming invasion of the site. In October 1962, the contract had been awarded to the German group headed by M/s.Lurgi of Frankfurt, for a price under £5 and a half million and a little time after that a few wooden huts appeared near the avenue of Shelton Abbey. After this “burst of activity” there seemed to be a further pause before the Civil Engineering people arrived to start the foundation stage. Now they were very busy, but nothing showed above the surface.
Welcome employment
Then suddenly Arklow had the strange sight of enormous weird pieces of plant and machinery being trundled through the town to be dumped on the site, and German technicians began to arrive. The show was in full swing! The rush of local employment was most welcome indeed in the town and surrounding areas because of the depression caused by the closure of Saint Patrick’s copper mines. The factory has now been over 8 years now in operation. Every year sees another extension or additional plant on the 100 acre site. With the official opening of four new plants last week the capital investment has trebled since 1962. Capital alone is not sufficient and credit for the success of such a venture is due in large part to human endeavour. The complex at Arklow is truly the work of many people who must feel a justifiable pride in the continued expansion at the Arklow works.
We used to make the embankments for the Carbon pond in NET, the Arklow Fertilizer factory probably around 1969 or ’70,and for the Gypsum pond would most likely have been around the 1972, period after NET began taking in Phosphate ore from Casablanca in Morocco, although the mines tailings pond had been used for short periods also ,and it was only in latter times when chatting to John McEvoy who used to work in the “Air Sep Plant”, from the start until it finished, who told me they used C bunker oil as the raw material to produce hydrogen after using Oxygen with it from the Air Sep plant, which went in with it into the reactor in the Gasification plant and by taking nitrogen from the air in the Air separation plant and by combining the two later were able to create NH3 Ammonia, using (“the Haber Process”) The factory used to run steam produced from the factory alongside the pipe carrying the bunker oil up from the harbour to keep it thin enough to pump up to the factory. The Carbon was a by-product and used in tyres and some was pumped as carbon slurry into the carbon pond, until they realized they had some of the best carbon in the world and could sell it using the Carbon Black plant for £3,000 per ton, which had to have been after October 1972, a little like the Canadians from around 1981 selling the elemental Sulphur which was a bi-product of oil refineries from the oil from the tar sands and some of the Alberta natural gas which was sour meaning it contained H2S, and sulphur was removed using the modified Claus process
and it never occurred to me to ask someone when I was sixteen or seventeen years old, how the carbon came about It was only in latter times after chatting to John , who told me about his time in the “Air Sep Plant” first and how it worked
There were four Regenerators in the Air Sep Plant short for Air Separation the Air Sep Plant was named 101
There were Two Nitrogen Regenerators and two Oxygen Regenerators
Compressed air ordinarily passes in through the nitrogen regenerator at about five atmospheres pressure, and nitrogen is exhausted through the re-generator at about 1-atmosphere pressure through a container filled with Quartz chippings
The G101 was the biggest generator in Ireland that drove the large compressor that took in the air something like 240 thousand cubic metres per hour product was going out for four minutes and then changed over to Air coming in for four minutes, product going out would be very cold going out through the Quartz Chippings and then coming in for 4 minutes warming the Quartz chippings, which would have been heating and cooling. The NET Booklet 1972 stated the (Low Temperature and Process techniques) of the Linde AG Processed a quantity of about 18, 700 normal cubic metres per hr of air and 3,500 normal cubic metres per hour of gaseous nitrogen (99.9% purity, atmospheric pressure dry) sent to the nitrogen gasometer, and produced 3,100Nm3/hr of gaseous oxygen (98% purity atmospheric pressure for the Gasification plant, John told me there were three oxygen oil free compressors, two working and one on standby, and Distillation was part of the process . According to the NET Book, the factory used the : The Shell Process which was suitable for the gasification of all Hydrocarbons by controlled non-catalytic partial Oxidation at a pressure of roughly 30 Atm.g. The product gas was mainly a mixture of hydrogen and carbon monoxide. NET stated two Shell reactors of the standard type were used which produced approximately 12,000NM3/hr of raw gas from roughly 4 tons of `Bunker-C oil. The oil feed and oxygen were preheated and, the admixture of high-pressure steam from a waste heat boiler, the feed mixture was converted in the reactor at a temperature of between 1, 000 to 1400 degrees C. The reaction temperature was controlled by the steam rate. The sensible heat of the reactor was utilized in a waste heat boiler for steam regeneration. Part of the Generated steam was used as gasification steam and for the preheating of oxygen and oil, while the major quantity was employed for CO Shift. The carbon formed during partial oxidation is separated from the cooled gas steam in a quench tube with water, whereby the carbon content of the gas is reduced to less than 1 mg/ Nm3. The carbon is separated from the slurry by the addition of oil, the carbon agglomerating with the oil to form carbon pellets (3- 15 mm. diameter). The pellets were used as fuel for a boiler generating additional high-pressure steam. The water leaving the pelletiser is free from carbon and was re-used in the process as a scrubbing medium for raw gas Conversion. The gas from the gasification plant had to go through desulphurisation in the Sulfinol wash unit the (Shell process) before going to the CO shift conversion Unit, To obtain a gas with high hydrogen content, carbon monoxide is converted catalytically with steam to CO2 whereby an equal volume of hydrogen is formed in accordance with the following equation :- CO + H₂O = CO2 + H₂. The factory was producing Carbon dioxide from this ,and after the CO Shift Unit and had to go then through the pressure wash to remove the CO2 formed in the Shift Unit, and then after this compressed nitrogen was admixed to the purified hydrogen gas from the pressure wash. After this the gas went through a copper solution scrubber where the residual CO and CO2 were removed to prevent harm or damage to the to the catalyst in the Ammonia synthesis, before going to the synthesis
Alan Fewster Wicklow People 21-Feb 1970 was the manager of the Ammonia plant also. A forty ton boiler was used to create the steam
The Sulphuric Acid Unit was operated by the classical contact process. The starting materials were elementary sulphur and hydrogen sulphide gas recovered from the Sulfinol wash unit in the Ammonia Plant.
The Sulphuric acid unit produced 212 tons per day of sulphuric acid of 98% strength, and high pressure steam (40 atm.g.). It had been designed and constructed so that it could also handle gases from the roasting of pyrites, in anticipation of the possibility of this material becoming available again from the copper mines at Avoca.
The elemental sulphur was melted and burnt in a furnace. Part of the heat of combustion was utilised for the production of high pressure steam (40atm.g 400 degrees C) in a subsequent waste heat boiler, this steam being fed to a turbo alternator. The sulphur dioxide formed was converted to sulphur trioxide in the convertor in the presence of vanadium pentoxide-containing catalyst. The heat of the reaction was used to preheat the incoming air. The SO3 gas leaving the convertor, after cooling by heat exchange with process air, passes to the absorption tower where it is absorbed by circulating sulphuric acid. The liberated heat of absorption heats up the sulphuric acid and is removed via a cooler in the acid circulation system. The hydrogen sulphide from the Ammonia plant was burnt with air in a furnace to form sulphur dioxide. Part of the heat of the combustion was eliminated from the gas in a subsequent radiation cooler. The gas was then sprayed with diluted sulphuric acid in a Venturi scrubber and cooled. The resulting mist was separated in a ceramic filter. The filtered SO2 gas was finally passed to the drying tower.
The process air for sulphur combustion as well as the SO2 gas from H2S combustion and waste gas neutralisation was sprayed in the drying tower with96% sulphuric acid and dried. The circulating sulphuric acid was heated by the absorption of water and cooled in irrigation cooler. The gas to be dried was passed through the drying tower and was passed to the sulphuric acid unit.
A constant acid concentration in the absorption and drying towers is maintained by exchange of acid between the two towers. The product may be withdrawn either from the absorption system or from the drying system. It can be mixed with process water for dilution.
A special feature of the Sulphuric acid plant was the tail gas treatment unit
This was designed to eliminate any harmful emissions of SO2 from the stack. This was the only unit of its kind in Ireland. In the unit the gas leaving the absorption tower was washed in a neutralisation tower with Ammonium sulphite/ bisulphite solution which absorbs the SO2 gas. The concentrated wash liquor is treated with sulphuric acid, whereby ammonium sulphate solution was stripped by air, and the SO2 thus separated was returned to the sulphuric acid unit, theSO2 free ammonium sulphate was pumped to the fertiliser plant for recovery as fertiliser. The neutralisation of the waste gas in conjunction with H2S combustion ensures that air pollution in the Avoca valley was kept a very low level, far below acceptable standards elsewhere at that time pre 1972.
The Plant was supplied by Lurgi Gelleschaft fur Chemie und
Huttenwessen mbh, Frankfurt (M).
13th October 1972 The Wicklow People quoted from what Alan Fewster said in the factory newsletter
What NET is doing to cut Pollution
Nitrigin Eireann has already spent well over half a million pounds in disposing of its waste products, says Mr A. Fewster in the latest issue of the company’s magazine “Network”. The article states that the company has had a responsible attitude towards pollution control and has installed specially designed equipment to reduce the effects of pollution. The capital cost of equipment was £ 400,000 and the additional cost of operating, maintaining and monitoring these facilities is estimated at about £35,000 per annuum. Mr Fewster outlines what steps N.E.T. has taken to reduce the pollution from its plants. The Ammonia Plant has a 200ft. high flare stack in order that unwanted gases could be burned and disposed of safely. The carbon slurry effluent problem was initially solved by the installation of a special furnace in which the waste carbon was burned. Unfortunately this combustion unit created a nuisance in the surrounding area and a carbon recycle system was installed in order that the unwanted carbon would be more clearly burned. However, this has given rise to process problems and further work is needed to improve the reliability of the new system. The ultimate solution will be to recover the carbon in a form suitable for sale and this is being actively pursued . the company is actively engaged.
No escape
Analysis carried out by ourselves and the institute of Research and Standards indicate that there is no escape of hydrogen fluoride from the phosphoric acid or C.C.F. plants. This is very satisfactory since there have been problems with this type of plant elsewhere.
Sulphuric acid plant
The Sulphuric acid plant is equipped with a tail gas treatment unit in order to remove Sulphur dioxide from the waste gases. It is interesting to note that in the United States many companies are at present, installing these units on their plants in order to meet the newly proposed limits on the discharge of Sulphur dioxide to atmosphere. A hydrogen sulphide transfer line and combustion unit were provided so that waste hydrogen sulphide gas could be burned and completely utilised on the Sulphuric acid plant without being discharged to atmosphere. New facilities were also provided to enable the hydrogen sulphide to be burned on the new Pyrites Roaster Unit. The new Roaster Unit has been equipped with a hot gas precipitator unit and stripper to ensure that the effluent is free of cinder and of low sulphur dioxide content. Facilities are provided for wetting the cinder to prevent it from being blown about. I can remember really well our CAT 930 loader becoming quite red and Hughie describing a man who was driving it getting out of the loader looking like a “Red Indian”, apparently if the red cinders were not dampened properly the red dust would dye everything red, and I remember how difficult it was for one of the fitters trying to repair a starter on the machine without destroying himself too much. The red cinder residue was hauled out close to an area beside the Roadstone jetty and was stored out in the open a bit like an open silage pit and was sold to a Dutch Firm , who used it for Iron, probably due to the fact it was from Iron pyrites. I had wrongly assumed the firm buying had been using it as some kind of dye. I knew the moisture content had to be monitored in the product before loading it on to the ship, because it could cause the ship to list with the motion out at sea
Damage to trees, covered in the same newsletter
The facilities provided at Arklow have considerably reduced the pollution problem in the area of the factory. The company carry out regular analysis both within the factory and outside. The results show that our stack effluents are generally satisfactory. However there are periods when conditions are difficult to control and some escape of gas occurs. This has caused some damage to conifer trees in the vicinity of the factory. Unfortunately the conifers are particularly susceptible to sulphur dioxide gas, however the damage due to sulphur dioxide gas would have been far more if the tail gas treatment plant had not been provided. A positive indication that there is little sulphur dioxide contamination around Arklow is the presence of the rose disease “Blackspot”. In large cities and industrial areas where appreciable sul-rose plants are rarely affected by Blackspot since the sulphur dioxide affects the fungus responsible for the disease
The Nitric acid plant has a stack and venturi system to dilute waste nitrous gases to recognised acceptable levels. It is interesting to note that the original acid plant had a catalytic tail gas unit installed at a cost of £44,000. This was a completely novel process but unfortunately was not very successful in operation and its use was abandoned. It is only recently after considerable effort and expenditure, that the process has now become feasible. The new nitric acid plant is of improved design and the rate of discharge of nitrous gases will be less than on the older plants.
NET used Gaseous ammonia and sulphuric acid in the saturator to create an Ammonium sulphate solution and ammonium sulphate crystals were formed by using oscillating centrifuges and they treated them after in a dryer cooler to end up with coarse crystals with good spreading properties.
N.E.T. had put in an application to the Council from 1968 to run a Gypsum pipeline out at the North beach to sea running out across the old dump, which I think may have been around where the present Starbucks restaurant or Aldi is at present, although Mick Carroll tells me there may have been a second dump up along that area. NET had jumped the gun a little by ordering their contractors to go in and clear the site of the old dump for assembling the pipeline on the 7th October 1970 before agreeing the type of pipe to be used with the Council engineer, I think I can remember Pat Flood RIP covering in some of the rubbish at times possibly for the Council, and it is possible he may have been on this job The Council accused NET of jumping the gun before deciding on the type of pipe to be used. One can really see “The Can-do attitude” in operation after the Arklow Chamber of commerce meetings involving RJ Kilgour, Avoca Mines General Manager, George O’Connor, Roadstone Manager at Arklow Rock, Brian Lenihan, Fianna Fáil, Godfrey Timmins, Fine Gael and Liam Kavanagh, the Labour party, all at the Annual Arklow Chamber of Commerce dinner in February 1970. The pile driving in July ’70 for the preparation of the site reserved in the middle of the factory for the Pyrite Roaster and completing the construction of the new road from the beech road into the back entrance of the N.E.T. Factory
in 1969 Discovery Mines, Limited expressed interest in operating the Avoca Venture as its North-West Territories gold mine was closing due to exhaustion of ore
The 16th March 1969 the Government option was exercised thus paving the way for Avoca Mines
In1969 N.E.T. Signed a contract for a new Pyrite Roaster.
The Pyrite Roaster plant was finished in March 1972, and Joe Murray photographed it 24th March 1972
In the Wicklow People 1972 Kevin Kearon , the Arklow harbour Board asked N.E.T. to help relieve congestion in the harbour by providing a pipeline to the lower jetty for discharging fuel oil cargo, and said it would help whether discharging or loading, three ships – fuel oil cargo, Ammonia, so three ships could be serviced at the same time. Mr Brendan Casey said that N.E.T. would draw up plans immediately. A photo of some of the pipes, which can be seen whilst walking from the Brigewater Shopping Centre up on to the 19 Arches, the the one with insulated covering most likely would have been for the heavy fuel oil and one of the four probably used for carrying Gypsum
1973 The Prilling Tower was built by John Paul & Co. Construction, using a system of continuous concrete pour Dick and Paddy Kavanagh of Kavanagh of Crane Hire Priced the Base for the Prilling Tower which was constructed in February 1973
Paddy spotted an opportunity for crane hire , and was an entrepreneur and purchased his first crane that year and by 1st August 1975, Feature in the Wicklow People, Paddy was taking delivery of his third crane, a new Coles 20-22 Telescopic crane
A ship on her maiden voyage from Casablanca in Morocco with a cargo of Phosphate of 2,100 tons arrived in Wicklow photograph appears in the Wicklow People 13th October 1972
Wicklow People 17 August 1973 NET Feature
It was stated when doing another piece on NET with Headline “Puts bubbles in your beer”
NET is conscious of the need to diversify its operations in the highly complex and difficult field of chemical process. Significant progress has been made in using by-products of the main process. Gypsum, a by-product of phosphoric production, will be used as raw material in the proposed Wallboard factory at North Quay, the export of Pyrite residue is another example of profitable use of a by-product. A major success is the profitable production of liquid carbon dioxide and dry ice, this is obtained from waste CO2 gas, generated as part of the ammonia manufacture process. The carbon dioxide product is distributed by associated Irish gases Ltd. They have a fleet of insulated pressure tankers which arrive at Arklow to fill up with liquid Carbon dioxide and then transport it to the customer’s premises. Delivery is effected over the whole country. The solid Carbon dioxide is sold under the name of “ARKOLD” and is transported in insulated containers to the depot at Inchicore. Associated Irish Gases then distribute the solid to the various users.
Brewing and mineral waters
About 80% of the liquid carbon dioxide sales go to the mineral water and brewing industries. In the production of mineral waters the liquid carbon dioxide is heated to convert it back in to the gaseous form the gas is then bubbled under pressure through water containing sugar and flavouring to produce the familiar fizzy drinks. The brewers use the carbon dioxide to increase the gas content of their brewed beers and lagers. All the well-known manufacturers use carbon dioxide produced at Arklow and it is of interest to note that your next pint of beer will doubtless contain bubbles which originated at “The Fert”
Horticulture
A recent application for liquid carbon dioxide is in horticulture. Commercial growers on the continent now realize that the addition of carbon dioxide to the atmosphere of their greenhouses can increase yields and considerably improve the form, colour and appearance of flowers. In Ireland at present only one or two growers are experimenting with carbon dioxide but it is hoped that when the benefits are more widely appreciated there will be an increasing demand for liquid carbon dioxide for this application. The solid carbon dioxide blocks have a temperature of-80 deg.C when heat is absorbed by the solid it is changed directly into carbon dioxide gas. No liquid is produced as with ordinary water ice.
Chilled meat, Arkold is an ideal refrigerant for the conservation of ice-cream. Small quantities of Arkold can do the same work as considerable quantities of ice and salt and owing to the absence of mess and corrosion of containers there is no risk of the ice cream product being contaminated. The main use of Arkold (about 50 per cent of production) is in the refrigerated container shipments of meat and other foods to England and the Continent. The chilled meat is loaded into special insulated containers and a special compartment is charged with Arkold blocks. Trials have shown that 250 lbs of solid carbon dioxide can keep six tons of chilled beef at about 36 deg. F. for three days. The consumption of Arkold varies from 30 tons per week up to about 60 tons per week in Autumn. In September and October, with the grass growth falling off, there is considerable increase in the number of beasts killed for the chilled meat trade. It is comforting to note that the increasing use of N.E.T. Fertilizers will produce more grass to produce more beef which will require more Arkold to ensure satisfactory product quality when delivered to the customer.
Booming freight business
N.E.T. has generated considerable road, rail and sea freight business in the area. There are upwards of cargo sailings per year between Wicklow and Arklow ports and Morocco, France, Spain and Holland in addition to coastal shipping. Phosphate, potash, china clay and other raw materials are imported while the export trade deals with nitric and sulphuric acid, pyrite residue and of course bagged fertilizer. Something in the region of 350,00 tons is handled by Arklow ports in the year. Moving this volume of tonnage to and from the factory provides contracts for a large number of hauliers, whose massive lorries constantly ply between the factory and the harbours. To cater for the volume of traffic generated, the company, in conjunction with Wicklow Co. Council constructed in 1970/71 a new access roadway from the Beech Road via the line of the old Monument Lane, passing by the Ralph Howard Pyramid Viscount of Wicklow
to the back entrance of the factory. This has relieved congestion in Arklow’s ever busy main thoroughfare, C.I.E. has its own siding located on the southern side of the river to handle the 130,000 tons dispatched annually by rail, requiring something in the region of 13,000 wagons. Special pallet wagons have been designed by CIE for the fertilizer trade and the long freight trains from N.E.T. comprise a large percentage of the rail traffic on the Dublin line. With further expansion of NET’S complex, a growth in all freight sectors may be expected
24th March 1972 Joe Murray takes photo of the Pyrite Roaster
13th October 1972Wicklow People has a Photo of a boat arriving in Wicklow Port with 2,100 tons of Phosphate for NET, around April 1972 the Gypsum pipe had burst about thirty feet from the beach and some of it ended up on the beach and drew a strong protest from the Arklow Urban Council when some of it ended up in a heap on the beach soiling it badly, and fortunately a wind took away a lot of the stuff. This would most likely be around 1972 that the Factory with phosphoric acid production most likely using the wet process reacting Sulphuric acid with the Phosphate ore. During 1973 The minister for industry and commerce Mr. Justin Keating opened a third nitric acid plant and the second calcium Ammonium nitrate plant, a pyrites roaster plant for sulphosphoric acid concentrator. The CCF plant would have been going strong in 1974 and made a high-quality granule like 10.10.20 for example with all three components contained in each Granule which would have given a very even distribution in the spread pattern across a field compared to a blended compound. It was evident from a dispute at Wicklow Port reported in the Wicklow People 1st November 1974
The dispute between N.E.T. Fertilizer factory at Arklow and 72 clerical workers worsened
This week and now the company may close down completely with 1,100 workers being laid off. The first steps in the close down were taken on Wednesday with the laying off of 100 workers in the Sulphuric acid, Phosphoric acid, and C.C.F. Plants and the number of lay-offs may be as high as 700 within a week, according to Mr. Peadar Mc Sweeney, general manager of the company.
The company state that they are not closing the factory but it is being forced on them as raw materials become scarce due to pickets being placed on cargo ships at Wicklow Port. Since Tuesday this week, the clerical workers have been manning pickets around the clock at Wicklow Port on a cargo ship of rock phosphate which is used in the three plants mentioned above. Already the Sulphuric acid and the phosphoric acid plants have completely shut down and it is only a matter of time until the C.C.F. Plant closes down completely. The company state that they are not closing the factory but it is being forced on them as raw materials become scarce due to pickets being placed on cargo ships at Wicklow Port. Since Tuesday this week, the clerical workers have been manning pickets around the clock at Wicklow Port on a cargo ship of rock phosphate which is used in the three plants mentioned above. Already the Sulphuric acid and the phosphoric acid plants have completely shut down and it is only a matter of time until the C.C.F. Plant closes down completely. One could easily see the CCF Plant and Sulphuric acid and phosphoric acid plants were going strong at this stage
The NET Fertilizer Factory appears to have found the solution for the Phospho Gypsum with an idea or a new concept for a Wallboard factory in Arklow August 1974
A year later in August 1975 it is called Arklow Gypsum and is advertising for Electricians and is in the final stages.
April 1975 The Wicklow People : the Danish Tholstrup Rosmuc Discharging Ammonia and two Ammonia ships anchored in the bay for the past two days entered the harbour to discharge their cargo after the fishing trawlers lifted blockade. Net Fertilizer factory importing Ammonia. N.E.T. had an original Ammonia Sphere with a Capacity of 1,000 tons and added a second Sphere with capacity for two thousand Tonnes ,which would most likely have been before the Marino plant bringing the total capacity up to Three thousand tonnes of Ammonia, perhaps someone will know what year it was. A photo of some of the old heavy fuel oil storage tanks on the North Quay and a stainless steel nitric acid storage tank
7 MAY 1976 The Wicklow People
NET Cork Plant not a Threat to Arklow
THE MULTI-MILLION POUND Ammonia and UREA PLANT of N.E.T., now under construction at Marino Point, Cork is not a threat to the future of the Arklow plant.
Justin Keating, Minister for Industry and Commerce, explained last Thursday at Arklow, that far from the Cork plant being in competition, it would be complimentary to the Arklow factory and make its future more secure. The Minister was speaking both at the opening of the new £3.3 million fourth nitric acid plant at N.E.T., which will produce 400 tons per 100 percent pure nitric acid a day, and up to a total of 1,000 tonnes per day and later to the Chamber of Commerce at Hoynes hotel.
This Cork project when on stream will give a guaranteed source of ammonia to ensure continued production and employment at Arklow, he said whereas hitherto the bulk of the company’s ammonia requirements was dependent on the uncertain supply situation abroad. The Kinsale Gas field with almost pure natural gas , Methane gas CH4, and producing hydrogen through steam reforming Methane gas would be more efficient and cleaner than the gasification of bunker oil. There wouldn’t any need for the Arklow NET Ammonia Plant after the NET Marino, Cork plant began sending Ammonia to Arklow by rail
IMPORTS
I am aware said Mr. Keating that there are problems for home producers at the moment because of the importation of substantial quantities of fertilizer this year, the bulk of which has come from the E.E.C.
“In the free trade situation, we must be prepared to compete with such imports. We must be competitive if we are to retain our home market and export to the community,” he said, and Mr. Keating added; however, if concrete evidence of dumping is produced, I shall arrange to have the matter investigated immediately “. He defended the use of natural gas from the Kinsale field for the production of ammonia at the Cork Plant, pointing out that it helps them produce fertilizer at very competitive prices. He chided some farmers who were taking the three weeks or three months’ perspective (instead of the three or thirty years) in going for the cheaper bag of imported fertilizer at the moment which was not in the long-term interests of the farmers
£24 million
Mr Keating who switched on the new nitric acid plant, said:” the company’s latest expansion is another chapter of the development of N.E.T. since its foundation in1961 “.
This 400 tonnes a day plant is the fourth nitric acid unit at Arklow gives the company a total production capacity of 1,000 tonnes of nitric acid per day, he said”. The total investment at Arklow is £ 24,000,000 compared with the original £6 million investment 10 years ago, stated Mr. Keating.
The rapid expansion in the use of nitrogen in Ireland will now allow N.E.T. to increase its N.E.T. nitrate capacity to over 400,000 tonnes per annum. One day’s nitrogen production from N.E.T. is now enough to fertilize some 8,000 acres of grassland. While at the N.E.T. factory Mr. Keating also met, and spoke with the worker’s action committee about the importation of fertilizer, which the action committee fear may threaten many of the 1,200 jobs at the factory.
Later Mr Keating went to see the N.E.T. subsidiary company, Arklow Gypsum Ltd., which will make plaster and plasterboard in the new factory on the North Quay, Arklow.
The commissioning of the plant commenced last week after problems with one of the tanks had been rectified with the installation of a new tank.
First in Europe
This factory will process waste chemical gypsum from N.E.T., which is currently being pumped out to sea.
The technology is new. The plaster manufacturing facility is the third of its kind in the world and is the first of its kind in Europe to process chemical gypsum to make plasterboard
The Plant, which will be in production later this year,(1976) is export orientated and when in full production will provide jobs for over 100 people.
The old Arklow Wallboard factory. I remember it having problems with a lot of reject wallboards made in the factory being brought out to the NET dump where we had either a Komatsu D50 bulldozer usually covering rubbish or if not with a CAT D6. I think British Gypsum who operated a Gypsum mine in Monaghan bought the equipment in it or may have even bought into the factory. The Boards were too heavy and hard I think, and could crack easily when a nail was driven in, although they did improve quite a lot after a year or so.
1979 NET Marino Point went into production making Urea fertilizer, and producing Ammonia from clean Natural gas and sending it by rail to Arklow ending the ammonia plant in Arklow and heavy fuel oil usage
June 1980: The Irish Independent “Arklow Gypsum and Southern Chemicals are combining the largescale production of Aerogyp. This is the first time that two Irish manufacturing firms have collaborated on insolation. The move reflects the national requirement for insulation, particularly for new houses, following the introduction of thermal insulation regulations last year. Argyps Aerogyp is an internal wall insulation system. It helps eliminate condensation and cuts heat loss through the walls by over 60 percent”. It was surprising after this it was due for closing at the end of September 1980, The fact that the Avoca mines was getting weak and closed in 1982, didn’t help this, as the source for Sulphuric acid production from the iron pyrites would have ceased. During 1987 Workers in NET Fertilizer factory rejected a merger with the ICI company.
NET Merger rejected by workers reported in the Wicklow People in 1987 and went ahead in October’87.
N.E.T. had an original Ammonia Sphere with a Capacity of 1,000 tons and a second Sphere holding two thousand Tonnes was added later, which was most likely before the NET ICI-merger bringing the total capacity of both Spheres at Arklow up to Three thousand tonnes of Ammonia, perhaps someone will know what year the second one was added.
1989 was the year this was taken, Joe Murray told me he is fairly sure 1989 was the year the Helicopter was hired, and Joe told me that was the only year John Holland was allowed into the parish grounds. Xavier McAuliffe. was the man who owned the helicopter and piloted it. McAuliffe, unfortunately was involved in a crash with the machine in Co. Kerry in 1992. One can see the Danish amber Tholstrup ship and the red gas container tanks in the old ERGAS plant beside the old Wallboard factory. The ERGAS cylinder filling plant plant began in 1971 employing well over 70 people when it was going well before it was bought for closure by Flogas in October 1989). due to falling sales of bottled butane gas.
Furious workers at the NET Factory in Arklow have refused to accept a joint venture between the giant chemical company ICI and the state fertilizer company. The deal which was approved by the cabinet on Tuesday provoked a strong reaction from I.T.G.W.U. branch secretary, Tommy Duffy who said on Wednesday that he had grave concerns about the details of the plan which could mean job losses at the Arklow plant. Following the announcement of the decision National group secretary from I.T.G.W.U. Led a delegation of worker’s representatives to the Department of Industry and Commerce to make it clear to Department officials that the deal would not receive the co-operation of the workers until commitments regarding the maintenance of jobs and continued investment in Arklow were given by the Minister. However, The Wicklow People has learned that not all the company’s four worker-directors voted against the proposal. And it’s understood that I.C.T. refused to retain any worker-directors on the joint venture Board. Instead, the existing worker-directors will be appointed to a holding company board which is feared will have no control over the running of the two companies.
This week one of the worker directors who voted against the proposal spoke out about the controversial deal which could lead to the diminishment of the Arklow operation. Mr. John Hoban speaking for the first time on the deal accused the government of allowing ICI to buy off one of Irelands state companies without contributing a realistic amount of finance to the project. “I can assure everyone that ICI did not make a contribution in line with the true value of the venture” he claimed. Mr. Hoban also charged the government with failing to keep its promise to consult the workers before approving joint venture plan which was concluded by the two companies last Summer. “They assured us that they would consult us first”, he fumed adding that the Government hadn’t even replied to a list of some 43 questions put to the Department of Industry and Commerce. A spokesman at NET in Dublin rejected workers’ fears that they will lose any say in the company. “The move of the worker-Directors to the holding company board will not undermine their position”, he asserted. The Spokesman added that worker-directors will continue to play an important role in the running of the company.
But he warned that Arklow only has a future in NET’S Plans so long as the plant remains competitive. He refused to say however how long the company perceived Arklow remaining viable.
By 1992 IFI had decided to upgrade their nitric acid production with the 5th nitric acid tower brought in June 1992 and Mark Kennedy wrote a very good piece in the Wicklow People called Gulliver’s travels’. This plant is called the 3600 and this time there is only a need for the fifth and fourth the 4400.
The fourth nitric acid plant tower was on 8th August 1975 an 80 ton 90 feet long absorption tower, which would produce 400 tons per 100 percent pure nitric acid a day
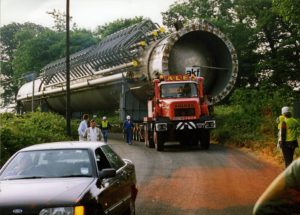
Michael Hetherington’s Pic. June92 5thNitric acid Absorption tower
And the 5th nitric acid huge 65 metre long Absorption tower, weighting 215 tonnes on21st June 1992, replacing existing units built in the early ‘70s, becoming more efficient producing about 900 tonnes of nitric acid per day and 900 tonnes with both Absorption towers combined and became more effective at reducing nitrogen oxide emissions, just as they were becoming really good at producing Calcium ammonium nitrate fertilizer and nitric acid in Arklow the cost of the Cork ammonium plant for using natural gas from the Kinsale field got out of control and ended up costing closer to 140 million, instead of its less than 40 million pounds estimate, would cripple them and unfortunately by 2002 a decision between the Government and IFI had been made to close the factory and sell off Arklow Cork and Belfast. The fact that the Kinsale gas field was beginning to run out in 200 was a real problem for producing Ammonia in the Cork plant
Apart from the large amount of Arklow Gypsum board rejects, the factory may have become aware of concerns of low amounts of Radioactivity that may occur in Phosphogypsum as a result of Phosphate ore being treated with Sulphuric acid as part of the production of phosphoric acid, and this may have been one more reason that played a part in the closure of Arklow Gypsum.
The modern sewage treatment plant officially opened May 9 2025, replacing the old Wallboard factory which lay idle for well over forty years , and the new Arklow Shipping offices using up the old redundant ERGAS Site